Технология производства
Доменный процесс – это совокупность механических, физических и химико-физических процессов, которые протекают в функционирующей ДП. Загружаемые флюсы, руды и кокс в процессе плавки превращаются в чугун. С точки зрения химии, это окислительно-восстановительный процесс. По сути, из оксидов восстанавливается железо, а восстановители окисляются. Но процесс принято называть восстановительным, так как конечная цель – получить металл.
Основным агрегатом для реализации процесса плавки служит печь (шахтная)
Крайне важно обеспечить встречное движение шихтовых материалов, а также их взаимодействие с газами, которые образуются во время плавки. Для улучшения процесса горения используется дополнительная подача кислорода, природного газа и водяного пара, что в совокупности называется дутьем
Основные марки чугуна
Чугун – сплав железа с углеродом. Содержание последнего элемента не должно быть меньше 2,14%. Помимо этого, присутствуют и другие элементы, такие как кремний, фосфор, сера и др. Углерод обычно находится или в связанном состоянии (цементит), или же в свободном (графит). Чугун можно поделить на следующие виды:
- Литейный – имеет маркировку Л1-Л6 и ЛР1-ЛР7.
- Передельный чугун – маркируется как П1 и П2. Если материал предназначается для отливок, то это ПЛ1 и ПЛ2. Металл с большим содержанием фосфора обозначается как ПФ1,ПФ2, ПФ3. Помимо этого, есть и высококачественный передельный чугун – ПВК1, ПВК2 и ПВК3.
- Серый – СЧ10, СЧ15, СЧ20,СЧ25, СЧ30 и СЧ35.
- Ковкий чугун – КЧ30-6, ЧК45-7,КЧ65-3 и др. Если после букв стоят цифры, то они обозначают временное усилие на разрыв.
- Легированный чугун, имеющий специальные свойства, обозначается буквой «Ч»;
- Антифрикционный (серый) – АЧС.
Можно говорить о том, что любой вид чугуна имеет свое дальнейшее назначение. К примеру, передельный используется для переделки в сталь и для производства отливок. В это же время марки ПЛ1 и ПЛ2 отправятся в литейный цех, а П1 и П2 будут использованы в сталеплавильном производстве.
Подготовка руды к плавке
Нельзя добыть железную руду из земли и тут же забросить ее в загрузочное устройство доменной печи. Сначала необходимо несколько улучшить технико-экономические показатели, что позволит использовать для получения чугуна относительно бедные руды, которых в земной коре значительно больше. К примеру, увеличение железа в руде всего на 1% приводит к экономии кокса на 2% и к увеличению производительности ДП на 2,5%. На первом этапе руда дробится на фракции, а дальше проходит грохочение. Последнее мероприятие необходимо для разделения железной руды по крупности. Дальше идет усреднение, где выравнивается химический состав. Один из самых важных и сложных этапов – обогащение. Суть процесса заключается в удалении пустых пород с целью увеличения содержания в руде железа. Обычно обогащение проходит в два этапа. Заключительным этапом является окускование, которое нужно для улучшения протекания плавки в доменной печи.
Доменное производство чугуна
Наибольшее применение нашел в производстве чугуна доменный процесс. Он включает ряд физических, физико-химических, а также механических проявлений, наблюдаемых в действующей доменной печи. Помещенные в эту печь исходные компоненты (кокс, железосодержащие материалы с флюсами) при прохождении всех операций преобразуются в сплав чугуна, выделяющиеся доменные газы со шлаками. Задача доменного производства чугуна – создание этого сплава из железосодержащих компонентов посредством их переплавления в доменных печах в очень высокой температуре.
Поэтому доменный цех – один из важнейших в структуре завода по производству чугуна. Помимо этого производство чугуна в доменной печи – основа для изготовления стали, прокатных изделий – конечной продукции металлургического цикла других предприятий. Часть чугуна является товарным продуктом, поставляемым в твердом виде в форме небольших слитков (чушек). Их получают на разливочных машинах, установленных в стороне от доменного цеха в специальном разливочном отделении. Другая часть чугуна идет на производство сталей. Газ, получаемый в ходе процесса производства чугуна, используют в мартеновском и коксохимическом производствах в металлургии. Он служит основным топливом нагревательных устройств прокатных цехов, доменных воздухонагревателей.
Чугун выплавляется в печах, куда помещаются, чередуясь слоями, железосодержащие компоненты с флюсами, топливом. От воздействия своей массы они спускаются в низ печи, куда в особые отверстия подается подогретый воздух под определенным давлением. Он поддерживает нужные условия горения загруженного кокса. Технологический процесс производства чугуна предполагает восстановление железа, а также других элементов из их окислов. В процессе восстановления кислород отнимают от окислов и получают из них компоненты или окислы меньшего содержания кислорода.
Одним из ведущих способов производства чугуна считается восстановление железа от действия окиси углерода. Она образуется от сгорания в горне печи природного газа. Еще стоит отметить, что восстановление железа, предусмотренное технологией производства чугуна для данных печей, осуществляется постепенно, в процессе поэтапного извлечения кислорода из окислов. Доменный процесс предполагает, что в процессе восстановления железа участвуют как окиси углерода, так и непосредственно сам твердый углерод.
Определенное количество железа также восстанавливается с помощью водорода. В схеме производства чугуна восстановление железа от действия водорода или окиси углерода считается непрямым (то есть косвенным), а восстановление с помощью твердого углерода называют прямым. На самом деле восстановление железа в данном случае осуществляется двумя стадиями. К моменту достижения железорудным составом зоны распада доменной печи, где установилась температура около 1000°С и больше, окислы железа успевают частично восстановиться непрямым путем в зоне, где действуют менее высокие температуры. В результате их прямого разложения углеродом получается полное восстановление железа.
Про науглероживание железа
Восстановленное в ДП железо поглощает в себя самые различные химические элементы и углерод в том числе. Как результат, образуется полноценный чугун. Как только он появляется в твердой форме, сразу же начинается его науглероживание. Сам процесс заметен при относительно невысоких температурах в 400-500 градусов. Кроме того, стоит отметить, что чем больше углерода в составе железа, тем ниже температура плавления. Однако когда металл находится уже в жидком состоянии, процесс протекает несколько интенсивней. Нужно понимать, что после того, как в чугуне будет окончательное количество углерода, изменить это уже будет невозможно. Такие элементы, как марганец и хром, способствуют увеличению содержания углерода, а кремний и фосфор уменьшают его количество.
Виды плавильных печей
Плавильные печи – оборудование, разработанное для переплавки, закалки, отпуска и отжига металлических предметов. Такие устройства требуются предприятиям как крупного, так и мелкого размера, например литейным цехам для переработки цветных металлов. Тогда в цехах могут перерабатывать в сутки от нескольких тонн и до нескольких килограммов сырья (в зависимости от вида обрабатываемого металла).
Самыми популярными плавильными печами в современной промышленности являются:
- Термические. Работают от теплоносителя – раскалённого воздуха или газа.
- Потоковые. Функционируют, благодаря электронно-лучевому излучению или плазме.
- Электрические. Вмещают в себя несколько разновидностей печей, работающих от электросети. Они бывают индукционными, муфельными, дуговыми и сопротивления.
- Муфельные печи выполняют поставленную задачу, благодаря мощным ТЭНам, накаляющим содержимое до сверхъестественной температуры. Печи сопротивления характеризуются воздействием тока на обрабатываемые материалы. Индукционные расплавляют металлы, путём воздействия вихриевых токов на перерабатываемое сырьё, а дуговые используют для работы электрическую дугу, вырабатываемую самим устройством.
По сути, электрические печи работают от единого источника питания, но при этом по-разному воздействуют на помещённое внутрь сырьё. Каждый из этих видов печей имеет вакуумную систему, благодаря которой металлические конструкции расплавляются быстрей и качественней. Рассмотрим особенности вакуумных печей и индукционных устройств, которые рационально применять при небольших суточных плавильных работах.
Достоинства и недостатки
Шахтный агрегат обладает такими основными преимуществами:
- Универсальность, доступность работы на разных видах топлива, в том числе и на жидком для модифицированных установок.
- Высокий КПД котла, производительность и автономность без дозагрузки топлива до 24 часов.
- Продуманная конструкция, упрощающая обслуживание, загрузка/выгрузка осуществляются через отдельные люки.
- Надежность и безопасность, поэтому загазованность помещения и отравление угарным газом, можно сказать, сведена на «ноль».
К недостаткам относят:
- повышенное сажеобразование и смолы при сгорании топлива;
- огромные габариты установки.
Меры предосторожности при эксплуатации
Перед розжигом нужно произвести тщательный осмотр механизмов, отвечающих за загрузку и выгрузку, воздуходувку, футеровку, дымосос, бункера, контрольные и сигнальные устройства, пылеочистительные и транспортирующие узлы, предохранительные ограждения. Печь останавливают при возникновении угрозы аварии, в случае прогорания футеровки, отсутствии топлива либо сырья. Остановка предваряется специальным сигналом, позволяющим своевременно перекрыть подачу материалов.
Кратковременная остановка сопровождается переходом на процесс естественной тяги, здесь необходима минимальная интенсивность загрузки сырья. Если требуется остановить механизмы на 2-3 суток, понадобится отключить разгрузку и дутье, герметизировать агрегат. Во время длительного простоя придется выгрузить рабочий материал из печи, освободить футеровки от привара клинкера.
В процессе работы печи важно координировать зону горения, отслеживать процесс обжига с применением контрольно-измерительного оборудования и сведений о сырьевой смеси, полученных из лаборатории. Шахтные печи активно используются в металлообрабатывающей промышленности, они незаменимы в процессе конечной переработки руды
Агрегаты используются в процессе обработки стали для формирования защитных покрытий на готовых изделиях. Это универсальные термические установки, способные выполнять широкий спектр производственных задач и потребностей различных масштабов
Шахтные печи активно используются в металлообрабатывающей промышленности, они незаменимы в процессе конечной переработки руды. Агрегаты используются в процессе обработки стали для формирования защитных покрытий на готовых изделиях. Это универсальные термические установки, способные выполнять широкий спектр производственных задач и потребностей различных масштабов.
Принцип работы
Подвергаясь постепенной сушке и нагреву, металл или шихта движутся сверху по направлению к низу установки. В свою очередь, разогретые газы, поднимаются снизу вверх, в противоход продукту, который заложен в подобную печку. Более наглядно этот процесс изображен на схеме:
При плавке цветных металлов, внизу печи устанавливается специальная емкость, куда стекает весь расплав, а выработанные агрегатом газы поднимаются наверх.
Проблемы шахтных печей в цветной металлургии состоят в применении особых видов шихты, а также дорогого и труднодоступного кокса. Сейчас такие процессы проводят с использованием газа и антрацитного угля, что значительно снижает себестоимость получения цветных металлов.
В работе шахтных печей для термической обработки сталей существуют свои особенности. В них металл не плавится, а подвергается температурной обработке для улучшения прочностных и антикоррозионных характеристик.
Проходя через стадии нагревания, с последующей обработкой в специальных средах с присутствием определенных газов, металлические поверхности приобретают, требуемые по технологическим условиям, свойства. К примеру, это процессы цементации или азотирования. Для них применяются специальные жаропрочные реторты.
Сколько стоит?
Цена на шахтные печи может колебаться в значительном диапазоне, в зависимости от многих параметров и их особенностей, которые были приведены в этой статье. Ниже представлено несколько моделей печей с краткими характеристиками и ценами на них:
- Серия агрегатов для цементации металлов СШЦМ, максимальная рабочая температура – 1000 градусов Цельсия, мощность 35 – 95 кВт, диаметры камеры от 600 до 2600 миллиметров. Цены на такие печи колеблются в районе нескольких сотен тысяч рублей и обговариваются индивидуально при заказе. Производятся в Украине фирмой Бортек.
- Печка закалочная с гидроприводом ПШЗ 15.30/12, цена ее составит 930000 рублей. Используется для нагрева легированных сталей для закалки, а также обжига изделий, максимальная рабочая температура – 1200 градусов Цельсия.
- Шахтные печи SC с принудительной циркуляцией атмосферы, изделия чешской компании LAC. Внутренний объем изделий колеблется от 500 до 1500 литров, мощность 50 – 120 кВт, размеры внутренней камеры от 800 до 1300 миллиметров. Работает от сети 400 вольт. Стоимость таких печей составляет более 1 миллиона рублей.
- Шахтные печи серии СШО, максимальная температура нагрева в них равна 800 – 1250 градусов Цельсия (в зависимости от модели), габариты рабочих камер составляют от 800 до 1500 миллиметров. Эти отпускные электропечи сопротивления используются для термической обработки металлов и сплавов в окислительной среде. Цена составляет 970000 рублей. Выпускаются в России научно-производственным объединением «Теплоконструкция».
Основные виды плавильных печей
В металлоплавильных агрегатах нуждаются не только гиганты черной металлургии, использующие вагранки, домны, мартены и регенераторные конвертеры с выработкой за один цикл в несколько сотен тонн. Такие величины характерны для выплавки чугуна и стали, на долю которых приходится до 90% промышленного производства всех металлов. В цветной же металлургии и во вторичной переработке — объемы значительно меньшие. А мировые обороты производства редкоземельных металлов и вообще исчисляются несколькими килограммами в год.
Но потребность в плавке металлопродукции возникает не только при ее массовом производстве. Значительный сектор рынка металлообработки занимает литейное производство, где требуются металлоплавильные агрегаты сравнительно небольшой выработки — от нескольких тонн до десятков килограммов. А для штучного ремесленного и декоративно‑прикладного производства и ювелирного дела находят применение плавильные аппараты с выработкой в несколько килограммов.
Все виды металлоплавильных устройств можно поделить по типу источника энергии для них:
- Термические. Теплоноситель — топочный газ либо сильно разогретый воздух.
- Электрические. Используют различные тепловые действия электрического тока:
- Муфельные. Разогрев помещенных в теплоизолированный корпус материалов спиральным ТЭНом.
- Сопротивления. Нагрев образца прохождением через него тока большой величины.
- Дуговые. Используют высокую температуру электрической дуги.
- Индукционные. Плавление металлического сырья внутренним теплом от действия вихревых токов.
- Потоковые. Экзотические плазменные и электронно‑лучевые аппараты.
Поточная электронно‑лучевая плавильная печь Термическая мартеновская печь Электро-дуговая печь
При небольших объемах выработки наиболее целесообразным и экономичным оказывается использование электрических, в особенности, индукционных плавильных печей (ИПП).
Производители
Рынок сталеплавильной электродуговой техники завален предложениями о поддельных, кустарных моделях по низкой цене. Поэтому планируя покупку, найдите в интернете сайт производителей подобной техники и закажите печи напрямую или через официальных дилеров. Покупая агрегаты у непроверенного продавца, вы рискуете приобрести некачественную и недолговечную конструкцию, пускай и за небольшие деньги.
Приведем краткий список компаний производителей электродуговых печей:
- Группа компаний «Thermal Technology» производит разнообразные по конструкции и мощности сталеплавильные агрегаты для лабораторных исследований и металлургической промышленности. Высокотемпературные печи могут проводить плавку в вакууме или при атмосферном давлении. Во всех случаях проводится тщательный контроль состояния воздуха в камере с расплавом. Технику используют не только в сталеплавильной отрасли, она успешно работает при выращивании монокристаллов и для получения оптоволокна.
- Российский производитель, компания «Оптим Толедо» выпускает электрические сталеплавильные печи для промышленных установок под маркировкой «ДППТ» и «ЭШП». Модели «ДППТ» – одни из самых мощных промышленных сталеплавийных электродуговых печей. В них собран весь запас конструкторов и эксплуатационников при проведении разработки проекта для плавильных устройств, работающих на переменном электрическом токе. Мощные преобразователи постоянного тока работают для обслуживания печей, модели ДСП.
- Дуговая сталеплавильная печь от Тайваньской компании «LEGNUM» – популярная марка производителей на российском рынке. Тиристорные электрические плавильные печи работают не только с металлами. Простота и надежность конструкции позволяет выполнять устройства в 2 вариантах. Они могут поставляться с гидравлической модификацией или редукторной. Отлично подходят для малого и среднего сталеплавийного предприятия с 3уровнем производительности свыше 2000 тонн в течение года.
- С 1989 года на российском рынке успешно работает научно – техническая компания «ЭКТА», специализирующаяся на выпуске термического промышленного оборудования. Научные методы, используемые при разработке и проектировании печей позволяют компании конкурировать с зарубежными производителями, особенно по соотношению цены и качества продукции. Дуговые печи переменного и постоянного тока могут использоваться для производства сплавов алюминия и других металлов.
- Печи от китайской компании «Чжэнчжоу Ланьшо промышленная печь» обеспечивают быструю плавку при пониженной себестоимости работы агрегата. Минимальные габариты при большом объеме загрузки, отличные показатели по теплоотводящим характеристикам и минимальный уровень загрязнения окружающей среды при полной загрузке и плавления шихты – это не полный список достоинств этой техники. Модели «KGPS 200кВт» применяются для производства нержавейки, чугуна, всех видов легированных, жаропрочных и конструкционных сталей. Можно использовать для получения цветных и драгоценных металлов.
Цены указывать нет смысла, они очень быстро меняются. Поэтому, советуем обратиться к производителям напрямую и узнать стоимость на интересующую вас технику.
Печи для приготовления и плавки литейных сплавов
Индукционная печь состоит из огнеупорного тигля, вмещающего в себя от 1 до 30 т расплава. Загружаемые в печь металлы нагреваются и плавятся за счет тепла, выделяющегося в самом металле при преобразовании в нем электрической энергии индуктируемой специальной обмоткой ( индуктором), окружающей тигель снаружи.
Дуговая вакуумная печь состоит из водоохлаждаемого тигля (кристаллизатора), изготовленного из сплава того же состава, что и выплавляемый в печи, или из меди. Кристаллизатор герметизирован и соединен с камерой, находящейся под вакуумом, что обеспечивает высокое качество получаемых в печи сплавов. Сплавы получаються при плавлении под действием электрической дуги расходуемого электрода.
Критерии выбора шахтных печей для плавки
Поиск оптимального оборудования основывается на эксплуатационных потребностях. Чаще всего агрегаты используются для нанесения на изделия из металла разнообразных покрытий, в этом случае будут оптимальными высокотемпературные модели с атмосферой защитных газов.
Шахтная печь СШЦМ-8.26/10
Для выплавки цветных металлов и обогащения руды подбирают агрегаты в зависимости от создаваемой ими температуры плавления. Размеры должны соответствовать планируемым объемам производства, здесь также важны габариты заготовок и деталей, которые предстоит отливать во время работы с печью.
Устройство шахтной печи
Большинство типовых агрегатов шахтного типа состоит из четырех основных частей, это:
- Блок загрузки материала;
- Блок выгрузки металла;
- Система дымоудаления (дымоход);
- Камера термической обработки (рабочее пространство).
Несколько примеров устройств разных типов шахтных печей:
- В процессе загрузки шихты или металла применяются механизмы конвейерного типа, а также кюбельные и скиповые устройства. Их выбор обусловлен различными моментами, такими, как тип загружаемого материала и условиями, в которых шахтная печь эксплуатируется. Самым универсальным вариантом является механизм скипового типа, в нем используется реверсный ковш и лебедка.
- Конструкция устройства для выгрузки готовой продукции состоит из нескольких блоков, основной ее частью является промежуточная накопительная емкость, которая, дозировано, подает и герметизирует продуцируемый материал.
- Система удаления выработанных газов состоит из нескольких патрубков, расположенных сзади шахтной термической установки. У современных моделей эта система довольна сложная, снабжена автоматикой и рядом фильтрующих элементов.
- Основная камера, в которой происходят процессы сгорания сырья и плавки (либо термической обработки) материала, имеет внешние органы управления. Оператор, обслуживающий подобное устройство, с их помощью задает нужные температурные режимы, согласно технологическим картам.
- Изнутри шахтная печь обычно футеруется, то есть обкладывается специальными огнеустойчивыми минералами или блоками из кирпичей. Лучшие огнеупорные материалы для шахтных печей – это шамотный кирпич, огнеупорное волокно и корунд.
Многие агрегаты с рабочими температурами до 1000 градусов снабжаются вентиляционными устройствами, устанавливаемыми над подом или в районе крышки печи. Они нужны для активного перемешивания газовой среды внутри термической камеры, а также для равномерного быстрого нагрева обрабатываемых изделий или шихты цветных металлов.
Еще кое-что интересное
Стоит обратить ваше внимание на то, что литейное производство использует металл, который был получен в доменной печи. По сути, при вторичной плавке получают изделия с требуемыми свойствами, которые изменяются в плавильной печи
В это же время отливки, химический состав которых оставляют неизменным в литейном производстве, изготавливают крайне редко. В частности это касается чугуна. Когда нужно получить деталь из черного металла, помимо чугуна, в печь загружают ряд модификаторов, флюсов, раскислителей, а также стальной лом и штыковой чугун. Последний нужен для получения стальных и чугунных отливок. Сам же процесс производства чугуна мало чем отличается от доменного производства.
Кто изобрел?
Дуговая электрическая печь, а именно эффект плавления металла с помощью электрической дуги был впервые показан отечественным ученным Поповым в начале 19 века. Такие опыты показали, что с помощью электродуговой установки можно не только расплавлять металл и стали, но и восстанавливать новые материалы из окислов при нагревании совместно с углеродистыми восстановителями. Эти опыты стали прародителем электрической дуговой сварки.
Но параллельно с Поповым, исследования проводились и зарубежными ученными. Уже 1810 году Дэви Гемфри была показана первая экспериментальная установка горения дуги, а в 1853 была осуществлена попытка построения первой плавильной печи Пишоном. 1878 – год, когда Вильгельмом Сименсом был получен патент на изобретение первой печи, работающей на электродуге. Но первая в мире сталеплавильная дуговая установка появилась только 1899 году. Поэтому, споры кто изобрел это устройство тянутся до наших дней.
Широкое применение в сталеплавильной промышленности таких устройств началось после окончания 2 Мировой войны.
Несколько фото электродуговых печей:
Текущие расходы
На одну тонну чугуна расходуется:
- 0,16 т кокса, что при цене 18000 р/т составляет 2880 р.
- 0,05 т известняка, при цене 2 250 р/т составляет 112, 5р.
- 0,025 т ферросилиция, при цене 30000 р/т составляет 750 р.
- 0,2-0,3 т стального лома, при цене 12000р/т составляет 2400 р.
- 0,7-0,8 т чугунного лома, при цене 9000 р/т составляет 8100 р.
Таким образом, на одну тонну чугуна расходуется сырья на сумму 14 242,5 р., на 118 т чугуна потребуется сырьё на сумму 1680615 р.
При трехсменной работе, когда в одну смену работают четыре человека, на зарплату им уйдет 630000 р. в месяц.
Расходы на электроэнергию за месяц составят 880 кВт*4=5280 р.
Итого сумма текущих расходов за месяц составит 2315895 р.
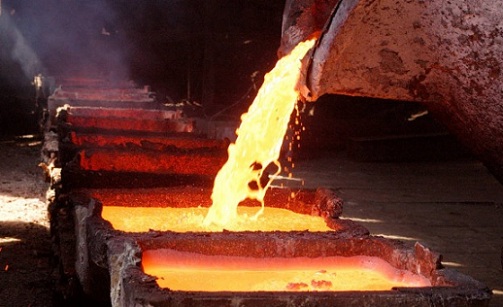
Индукционная тигельная электропечь
Существует много разновидностей данных устройств, но индукционная тигельная печь – это самое технологически выгодное оборудование, востребованное большинством металлургических предприятий. Такие печи основаны на принципе воздействия электромагнитного поля непосредственно на расплавляемый металл, которые возникают вследствие индукции тока большой частоты.
За счет такого принципа работы достигается максимальная равномерность распределения тепловой энергии по всему пространству обрабатываемого материала, что полностью исключает перегревание металла на протяжении всего процесса плавки. В дополнение, это способствует получению максимально однородной структуры.
Критерии выбора шахтных печей для плавки
Поиск оптимального оборудования основывается на эксплуатационных потребностях. Чаще всего агрегаты используются для нанесения на изделия из металла разнообразных покрытий, в этом случае будут оптимальными высокотемпературные модели с атмосферой защитных газов.
Шахтная печь СШЦМ-8.26/10
Для выплавки цветных металлов и обогащения руды подбирают агрегаты в зависимости от создаваемой ими температуры плавления. Размеры должны соответствовать планируемым объемам производства, здесь также важны габариты заготовок и деталей, которые предстоит отливать во время работы с печью.
Индукционные печи своими руками
Среди имеющихся распространенных методик создания таких агрегатов можно найти пошаговое руководство, как сделать индукционную печь из сварочного инвертора, с нихромовой спиралью или графитовыми щетками, приведем их особенности.
Агрегат из высокочастотного генератора
Она выполняется с учетом расчетной мощности агрегата, вихревых потерь и утечек на гистерезисе. Питание конструкции будет идти от обычной сети в 220 В, но с использованием выпрямителя. Такой вид печи может идти с графитовыми щетками или нихромовой спиралью.
Для создания печи потребуется:
- два диода UF4007;
- пленочные конденсаторы;
- полевые транзисторы в количестве двух штук;
- резистор в 470 Ом;
- два дроссельных кольца, их можно снять со старого компьютерного системщика;
- медный провод Ø сечения 2 мм.
В качестве инструмента используется паяльник и плоскогубцы.
Приведем схему для индукционной печи:
Индукционные портативные плавильные печи такого плана создаются в следующей последовательности:
- Транзисторы располагаются на радиаторах. Из-за того, что в процессе плавки металла схема устройства быстро греется, радиатор для нее нужно подбирать с большими параметрами. Допустимо устанавливать несколько транзисторов на один генератор, но в этом случае их нужно изолировать от металла при помощи прокладок, сделанных из пластика и резины.
- Изготавливаются два дросселя. Для них берутся два заранее снятые с компьютера кольца, вокруг них обматывают медную проволоку, количество витков ограничено от 7 до 15.
- Конденсаторы объединяются между собой в батарею, чтобы на выходе получилась емкость в 4,7 мкФ, их соединение проводится параллельно.
- Вокруг индуктора обвивается медная проволока, ее диаметр должен быть 2 мм. Внутренний диаметр обмотки должен совпадать с размером используемого для печи тигля. Всего делают 7-8 витков и оставляют длинные концы, чтобы их можно было подключить к схеме.
- В качестве источника к собранной схеме подсоединяется аккумулятор мощностью 12 В, его хватает примерно на 40 минут работы печи.
Если необходимо, то делается корпус из материала с высокой термоустойчивостью . Если же выполняется индукционная плавильная печь из сварочного инвертора, то защитный корпус должен быть обязательно, но его нужно заземлить.
Конструкция с графитовыми щетками
Такая печь используется для выплавки любого металла и сплавов.
Для создания устройства необходимо заготовить:
- графитовые щетки;
- порошковый гранит;
- трансформатор;
- шамотный кирпич;
- стальная проволока;
- тонкий алюминий.
Технология сборки конструкции заключается в следующем:
- Выполняется основа – в виде бокса, который изготавливается из шамотного кирпича, его кладут на огнеупорную плитку.
- Сверху бокса укладывается лист асбестокартона, если ему нужно придать определенную форму, его поверхность нужно смочить водой. Чтобы конструкцию сделать жесткой, нужно обмотать ее проволокой. Размеры бокса зависят от мощности трансформатора. Лучше всего использовать его из сварочного аппарата. Если он большой мощности, то его следует перемотать.
- Во избежание перегрева трансформатора его обматывают тонким алюминием.
- На дне кирпичного бокса располагается глиняная подложка, чтобы расплавленный металл не растекался.
- Устанавливаются графитовые щетки.
Прибор с нихромовой спиралью
Такой прибор используется для выплавки больших объемов металла.
В качестве расходных материалов для обустройства самодельной печи используется:
- нихром;
- асбестовая нить;
- кусок керамической трубы.
После подключения всех составляющих печи по схеме, ее работа состоит в следующем: после подачи электрического тока на нихромовую спираль, она передает тепло металлу и плавит его.
Создание такой печи проводится в следующей последовательности:
- Навивание спирали, для нее используется проволока диаметром 0,3 мм, длина заготовки должна быть около 11 метров.
- Проволока наматывается вокруг длинной трубки, ее диаметр – 5 мм.
- Кусок трубы из керамики выступает в качестве тигля, его подрезают до нужного размера, примерно на 15 см. В один его конец вставляется асбестовая нить, чтобы расплавленный металл не растекался.
- Укладка спирали вокруг трубы. Между ее витками укладывается асбестовая нить, она ограничит доступ кислорода и тем самым не допустит замыкания в печи.
- В таком виде катушка помещается в лампу высокой мощности, в ней имеется патрон нужного диаметра, который чаще всего изготовлен из керамики.
Такая конструкция отличается высокой производительностью, она долго остывает и быстро нагревается. Но необходимо учесть, что если спираль будет плохо изолирована, то она быстро перегорит.
Меры предосторожности при эксплуатации
Перед розжигом нужно произвести тщательный осмотр механизмов, отвечающих за загрузку и выгрузку, воздуходувку, футеровку, дымосос, бункера, контрольные и сигнальные устройства, пылеочистительные и транспортирующие узлы, предохранительные ограждения. Печь останавливают при возникновении угрозы аварии, в случае прогорания футеровки, отсутствии топлива либо сырья. Остановка предваряется специальным сигналом, позволяющим своевременно перекрыть подачу материалов.
Кратковременная остановка сопровождается переходом на процесс естественной тяги, здесь необходима минимальная интенсивность загрузки сырья. Если требуется остановить механизмы на 2-3 суток, понадобится отключить разгрузку и дутье, герметизировать агрегат. Во время длительного простоя придется выгрузить рабочий материал из печи, освободить футеровки от привара клинкера.
В процессе работы печи важно координировать зону горения, отслеживать процесс обжига с применением контрольно-измерительного оборудования и сведений о сырьевой смеси, полученных из лаборатории. Шахтные печи активно используются в металлообрабатывающей промышленности, они незаменимы в процессе конечной переработки руды
Агрегаты используются в процессе обработки стали для формирования защитных покрытий на готовых изделиях. Это универсальные термические установки, способные выполнять широкий спектр производственных задач и потребностей различных масштабов
Шахтные печи активно используются в металлообрабатывающей промышленности, они незаменимы в процессе конечной переработки руды. Агрегаты используются в процессе обработки стали для формирования защитных покрытий на готовых изделиях. Это универсальные термические установки, способные выполнять широкий спектр производственных задач и потребностей различных масштабов.
Заключение
Сделаем несколько важных замечаний.
Литейное производство относится к числу взрывоопасных и пожароопасных, кроме того, оно сопряжено с выбросом большого количества вредных веществ. Поэтому лицензирование его в России сопряжено с известными трудностями и затратами.
Функционирование такого производства требует повышенной технологической дисциплины и неуклонного соблюдения правил техники безопасности.
Характерным отличием литейного процесса является огромная роль, которую играет технически грамотный персонал, особенно это касается инженерно-технических работников. Поэтому к подбору их надо подходить с большой ответственностью и не скупиться на достойную оплату их труда.
Так же следует отметить большие резервы рентабельности, которыми обладает литейное дело в России. В основном они базируются на внедрении новых технологий и развитии производственной инфраструктуры, а так же на расширении ассортимента выпускаемых изделий.
Например, сейчас очень активно развивается внедрение новых видов форм, систем нагрева и поддува.
Что касается ассортимента, то при работе вагранок, как правило, 10% выпускаемой продукции составляет стальное литьё, которое гораздо дороже чугунного. Зачастую вагранку используют так же для выплавки цветных металлов.
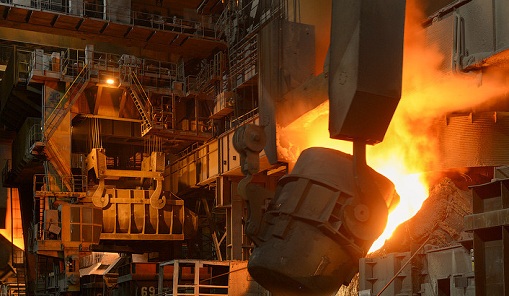
- В индукционных печах нагревание металла происходит за счет электромагнитного поля, возникающего между индуктором и металлом, отделенным от него огнеупорной стенкой. Производство отливок из чугуна в индукционных печах тоже часто используются малым бизнесом, иногда они работают в связке с вагранками.
- В дуговых печах нагрев происходит за счет электрической дуги большой мощности, температура которой достигает 3000 градусов. Дуга эта возникает между металлом и электродом. В таких печах осуществляется производство чугуна и стали в больших объемах.
- В плазменных печах нагрев происходит потоком газа раскаленного в плазмотроне до 5000-15000 градусов. Они применяются для выплавки специальных сталей.